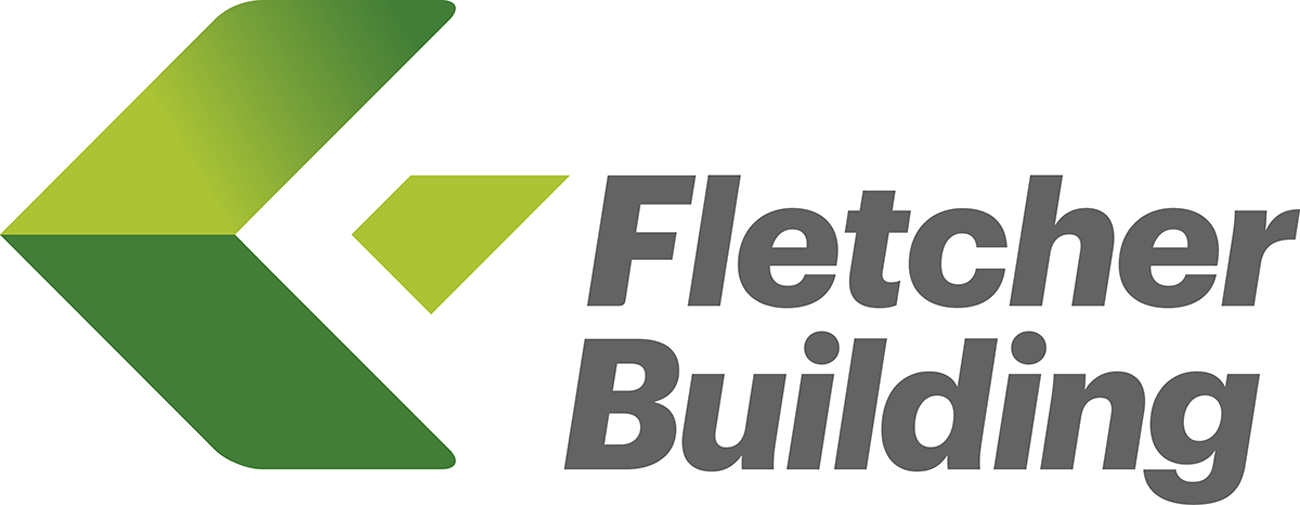
They’re reimagining how we build and care for our homes by repositioning ‘building interiors as a service’. By using a framework of closed loop systems they can ensure products like MDF can become a reusable, valuable commodity that benefits customers and the environment.
Fletcher Building is now one of the leaders in manufactured building products. From the insulation in our walls that keeps us warm, to the foundations of the buildings we live and work in, through to the interiors of our kitchens, offices and shared spaces. The Fletcher Building brought a team drawn from multiple parts of their business. At XLabs they explored what the next 100 years might look like – and what their role as industry leaders could be.
The challenge they wanted to solve is below the surface. It’s at the core of many objects and interiors, at the core of our table tops, our kitchen cabinets and our office desks. This core is MDF – medium-density fibreboard that is effectively wood fibres glued together to form a board. They found out that 90% of MDF used, ends up in landfill. In talking to their fabricators to understand where this comes from, one mentioned that they were generating ½ tonne of MDF each day. Another fabricator said that 9 out of 10 of their kitchen projects are renovations, customer desire to renew their space leading to the old kitchens potentially going straight to landfill.
The challenge Fletcher Building tackled at XLabs was -
How might we solve the reuse, recycling and remanufacturing of wood products in residential construction for the NZ environment?
- By using smart materials and technologies, we could make MDF from renewable, natural alternatives.
- By networking participation with third parties, the MDF offcuts and discards could be reused.
- By recovering the core materials ourselves, we could remanufacture MDF into new products.
- Another solution would be to turn these MDF waste streams into something completely new, like a fibre insulation product.